Production
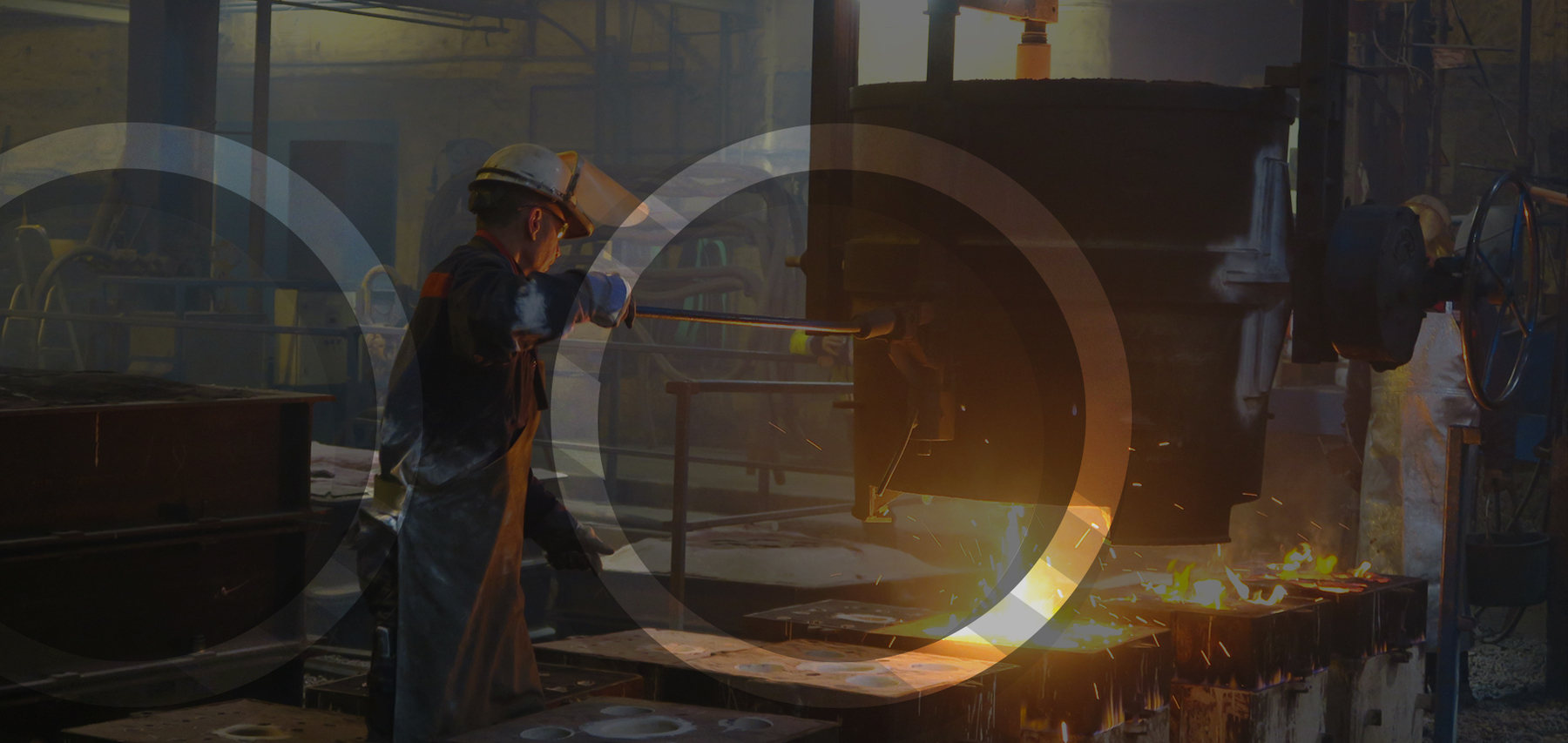
Casting, machining, assembly
Österby Gjuteris production is as far away from an assembly line as you can get, since most products are only produced a couple of times. This puts a lot of demands on knowledge, experience, materials and access to skilled workers. We have an extensive tool and machine shop, and software’s for design, programming and simulations. Below you can follow the different steps of our production facility.
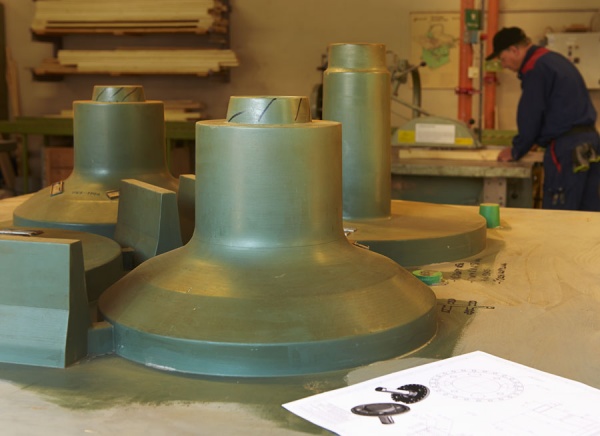
Pattern shop
In the pattern shop we are manufacturing smaller patterns in wood or styrofoam, repair and change existing patterns. We also do regular measurements of new patterns.
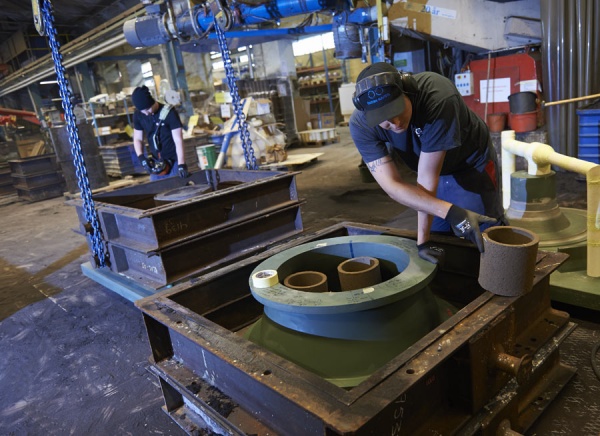
Molding and core making
Sand molds and cores are made with hand molding technique. The sand is olivine or chromite sand with cold hardening bonding agent. In the molding and core hall there are three sandmixers.
After casting 90% of the sand is recycled and the chromite sand is separated from the olive sand. The molds and cores are washed either by paintbrush, flow or spray.
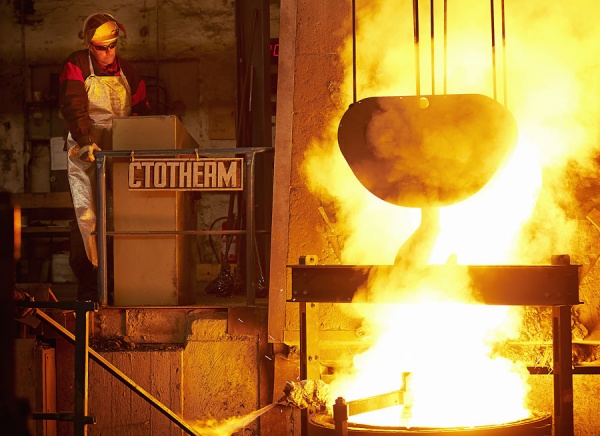
Melting
The three HF-smelting furnaces have a total capacity of approximately 9 tonnes. Casting is made with bottom pouring ladles in different sizes from 1,5 tonnes up to 10 tonnes. All melts are analyzed in a light emission spectrometer to ensure the melts composition.
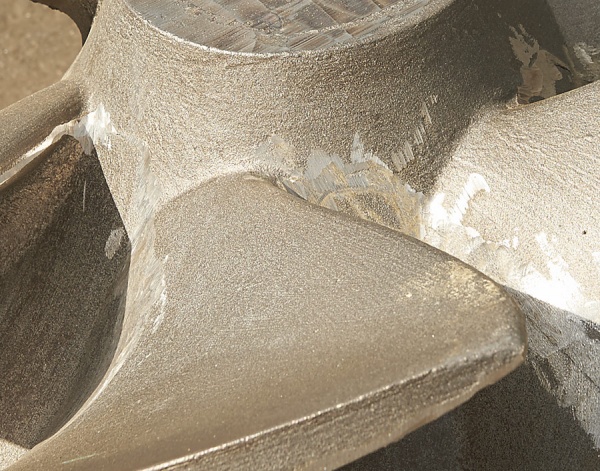
Blasting and cutting
After the casting is removed from the sand mold it is blasted in a steel shot blaster. We also have a sandblaster. After blasting the feeders and ingots are cut of to be recycled and melted down again.
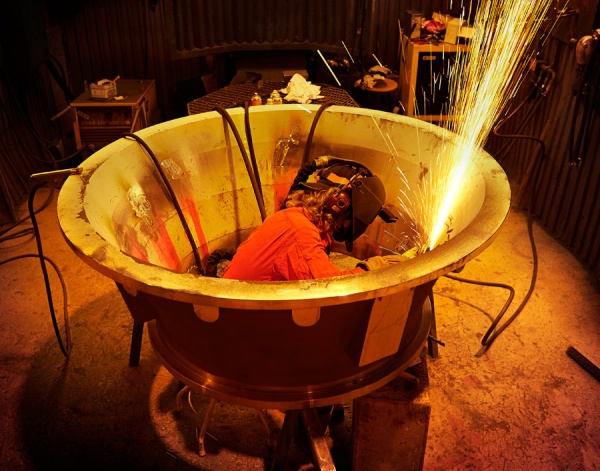
Fettling
After blasting and cutting the castings are fettled by grinding to remove any parts of the old feeders and ingot and prepare the casting for a possible machining.
In the fettling shop the employees can handle several welding procedures for different grades and welding techniques. We have procedures for pressure vessels.
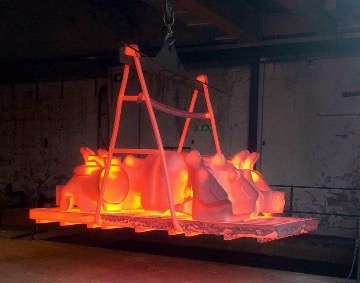
Heat treatment
Österby Gjuteri has two gas powerd heat treatment furnaces for temperatures up to 1 225°C with controlled atmospheric pressure and a computer logging the temperature. We use air or water as cooling media.
The heat treatment is essential for the steel properties, the procedure differs depending on the wanted property.
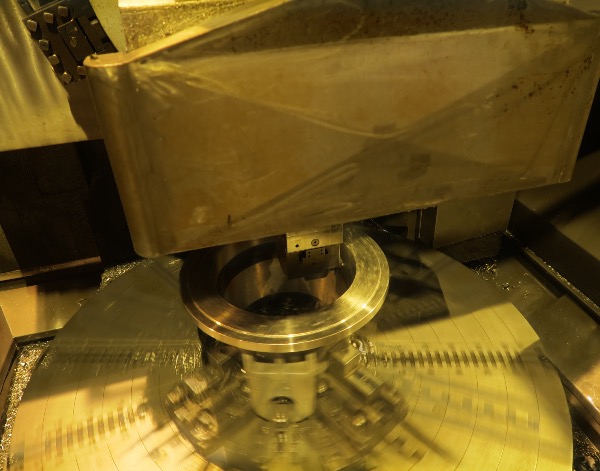
Machine shop
The steel castings are machined using CNC-milling and drilling machines. From the machine shop the products can be delivered rough machined or finished machined.
The operators are programming the machines themselves.
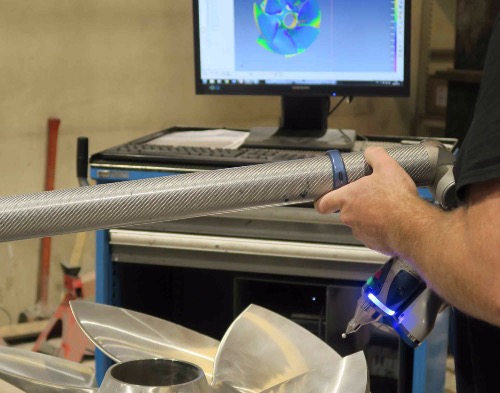
Testing and control
The control department secures that the castings is of right quality during the production and before delivery.
Control measurements are made with traditional instruments and with modern measurement arms. With the help of the measurement arm we can probe or scan a product and compare with a 3D-file.
Our operators are certified at level 2 for PT (Dye penetrant), MT (Magnetic particle inspection) and UT (Ultrasonic inspection). X-ray is made by third party in our X-ray bunker.
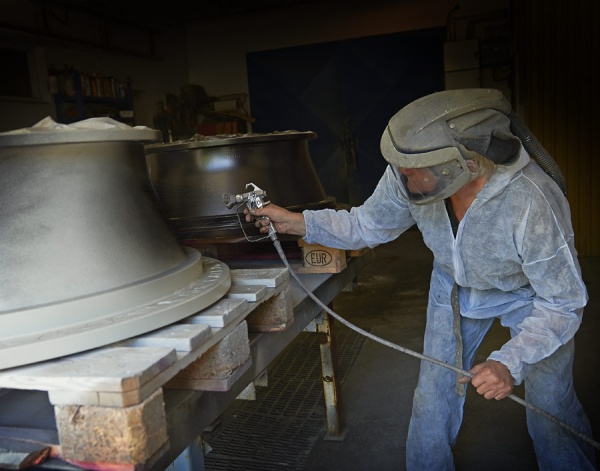
Painting and assembly
In addition to casting, machining and quality control, many of our customers gives us the opportunity to assemble and paint their products that then can be delivered completely finish to our customer – or to our customers customer.